Challenges and Best Practices in Material Handling in Mining: Adaptability, Efficiency, and Performance
Material handling plays a central role in the operational performance of any mineral processing plant. More than simply transporting ore between processing stages, it’s about ensuring that material flows with control, reliability, and in a manner compatible with the physical and chemical characteristics of each ore type. Over the life of a mine, this challenge becomes even more complex, especially as new mining fronts and reserves are brought into operation.
Equipment Adaptation to Mineral Variability
It is common to observe significant changes in the characteristics of ores from different mining zones over time. Variations in hardness, natural moisture, abrasiveness, and especially ROM (Run of Mine) granulometry directly affect the efficiency of crushing, screening, and grinding systems. Equipment originally designed for one ore type may not perform well with new materials, leading to frequent blockages, crusher overloading, and increased energy consumption.
Therefore, material handling systems must be designed and operated with flexibility, allowing quick adjustments, such as screen changes, crusher gap regulation, deck modifications, or even bypass routing, to handle varying ore types while maintaining process stability.
Process Composition Impact: Water, Residence Time, and Efficiency
Another critical factor in material handling lies in maintaining a proper balance between water addition and material residence time in screens, classifiers, and thickeners. Excess water can impair screening, allowing unwanted fines to pass through and reducing separation efficiency. Conversely, low moisture operation may cause blockages, increase equipment wear, and complicate conveyor and chute transport.
Incorrect residence time in vibrating screens, hydrocyclones, or other classification equipment can seriously compromise process selectivity, leading to rework, product losses, and downstream overloads. This all translates to lower productivity, higher energy consumption per processed ton, and ultimately, financial losses and failure to meet throughput targets.
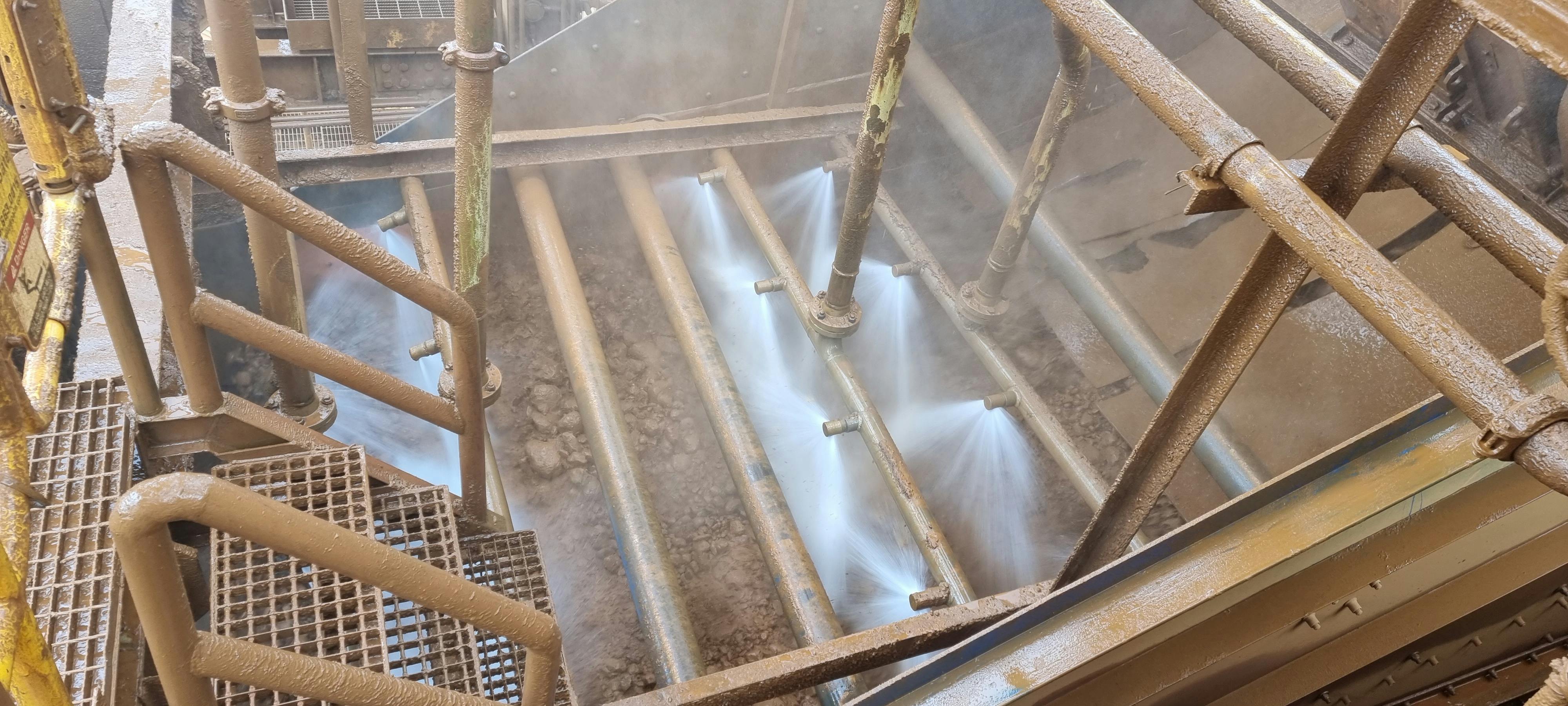
Integration Between Engineering and Operations
To tackle these challenges, continuous communication between process engineering, maintenance, and operations teams is essential. Constant monitoring of key indicators, such as throughput, particle size distribution, moisture levels, and equipment performance (availability and utilization), enables real-time adjustments and more effective corrective action planning.
Digital tools and real-time control systems, such as online particle size analyzers, belt scales, and SCADA systems, are already in use in modern plants, allowing predictive actions and greater operational reliability.
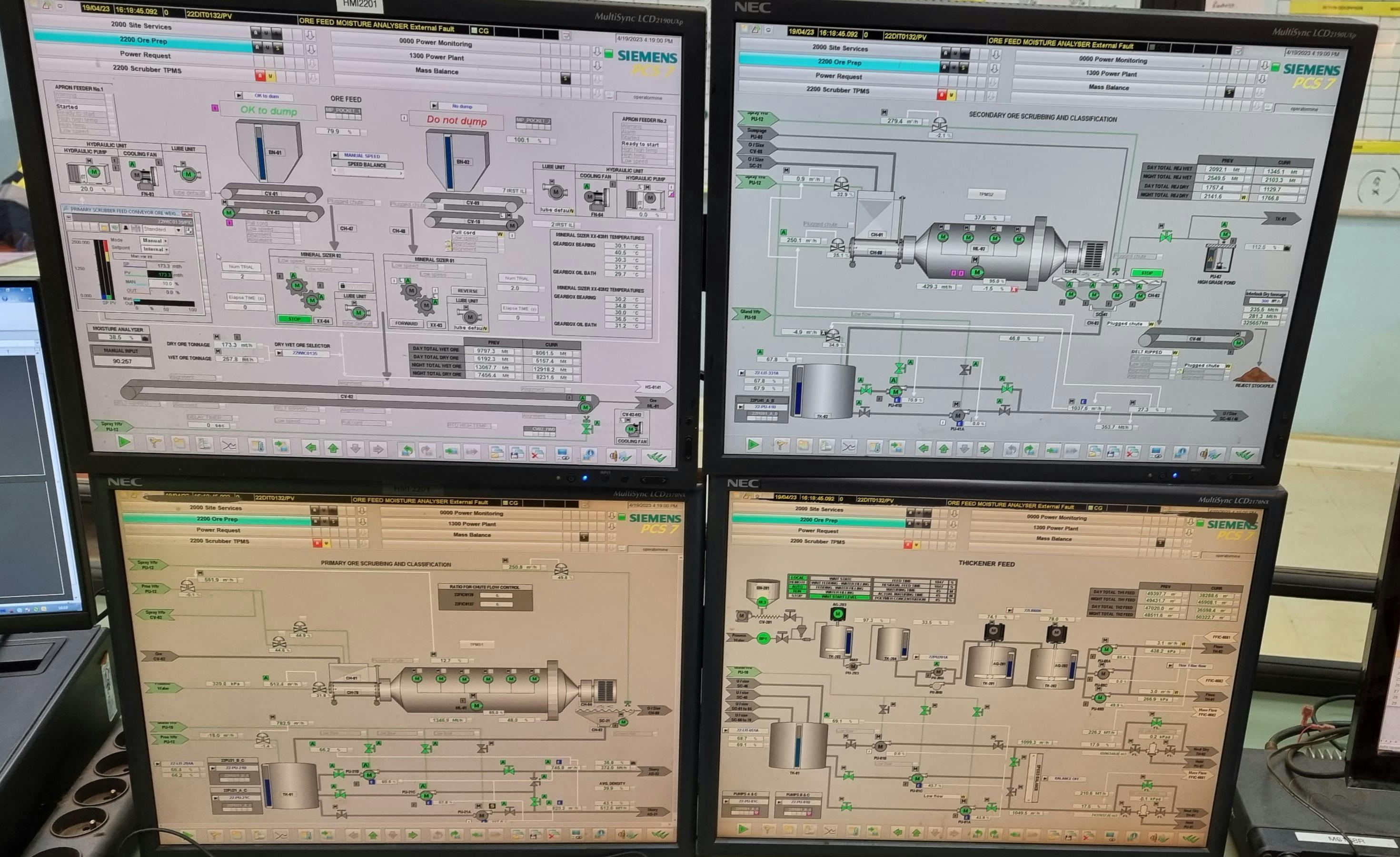
Other Relevant Factors
In addition to the points mentioned above, other important variables include:
- Accelerated wear of conveyors and chutes, especially when transitions are poorly designed or transport speed is inadequate;
- Material build-up in transfer points and silos, which can cause blockages and reduce productivity;
- Environmental aspects, such as dust generation and spillage, which can be mitigated with enclosures, sprinklers, and suppression systems;
- Ergonomics and operational safety, particularly in areas involving manual material handling or access to critical maintenance points.
The success of a mining project is directly linked to the plant's ability to adapt its material handling systems to constantly changing scenarios, both in terms of ore quality and operational conditions. Flexibility in design, smart automation, predictive maintenance, and process composition control are key elements for ensuring productivity, safety, and financial return.
At Plus Natural Resources, we have a strong track record of increasing productivity in processing plants by leveraging the deep experience of our specialists. With years of hands-on knowledge, we help revive underperforming operations, eliminate bottlenecks, and unlock the full potential of mineral beneficiation plants.